construction surveys
Construction surveys that enable the plans of proposed new structures
What We Do at GSMS
Setting Out
Transferring a building design from plan to site – establishing the key components to ensure complete accuracy.
Site Control
Making sure a building takes shape according to plan, in a safe and efficient manner.
Structural Monitoring
Determining the movement of a building using a network of non-invasive control points located outside.
As Built Survey
Ensuring all aspects of a project have been constructed correctly and conform to the site plan.
Setting Out
Setting out is the transference of a building design from plan to site – establishing the key components for the structure to ensure complete accuracy. It literally ‘sets out’ the foundation and the skeleton for the entire structure. Setting out creates the physical positions of corners and walls of a structure. For example, the steel frame on a retail park needs a grid for the columns so the fabricators can locate and work from the centre points.
With large scale projects, such as high rise buildings and developments, a succession of setting out surveys may be needed as construction progresses. For example, during enabling and earth works stages or as utilities and the actual structure itself develops. Essentially, setting out will help the construction team build according to the current plan.
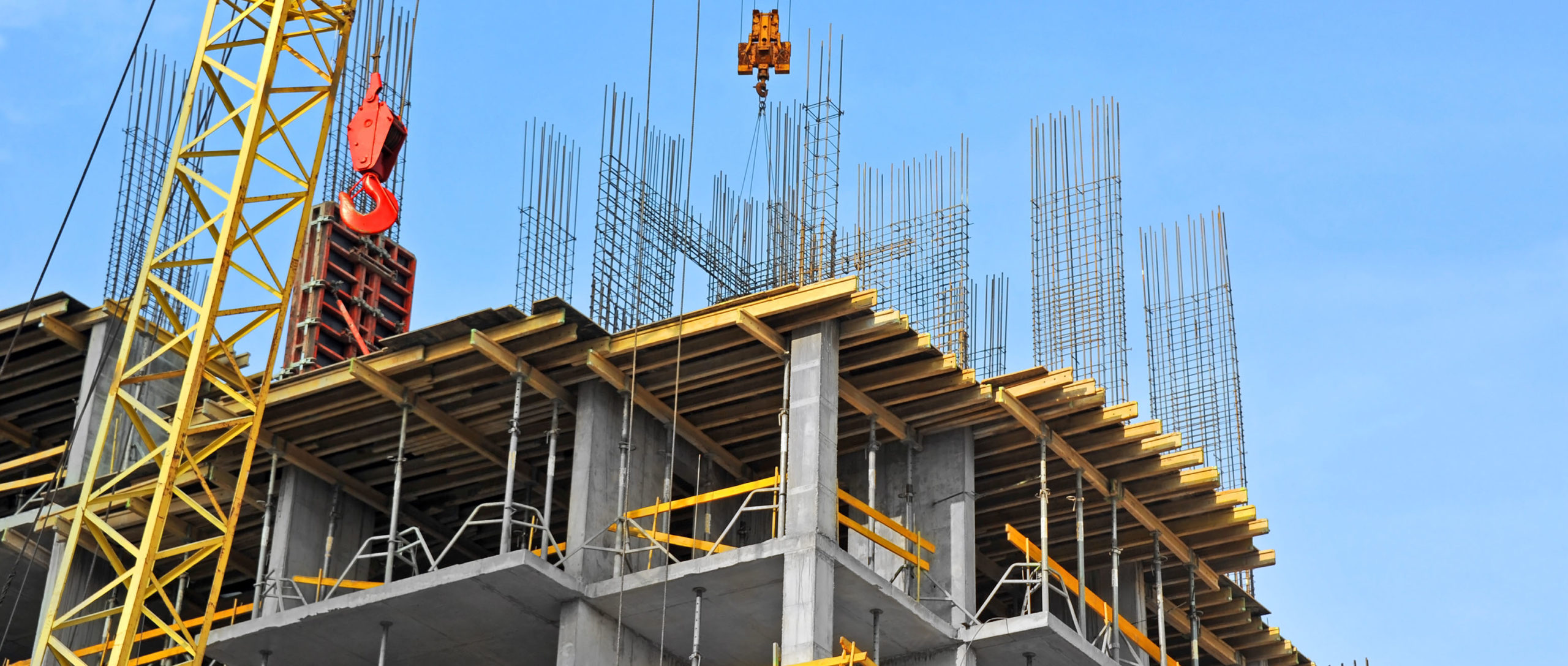
the technology we use
key points to consider
Our philosophy is to make setting out a valuable service for our clients:
- Ensures the construction team has the relevant points on site to enable them to build according to plan.
Minimises disputes further down the line. - Appropriate for all kinds of construction: small dwelling, extensions to existing buildings, major commercial buildings and high rises, infrastructure such as roads, bridges, tunnels etc, precise positioning of M&E equipment.
Our attention to detail makes us an ideal choice for client-requested independent audits.
site control survey
A robust site control survey will enable construction to progress according to the plan. This includes off-site construction (eg a bridge) where the tolerances can be as little as 6mm. And, of course a site control survey will manage any changes to the plan.
How the site control survey works
GSMS has an ‘all surveys’ procedure for every job. This is a robust frame-work for mapping accurately a range of construction projects from individual houses to major engineering systems such as: underground utilities, roads, power lines, tunnels, and many other high precision projects. We use high grade, well maintained instruments together with excellent survey practice.
An important part of a site control survey is primary control which we establish and maintain at every stage of a project. We also set up secondary network stations and, where necessary, supplemental control points. We use GNSS systems combined with properly calibrated total station and level instruments. And, finally good geometry.
Our clients’ design information can be input directly into our instruments, enabling us to establish survey control networks using the engineer’s setting out criteria.
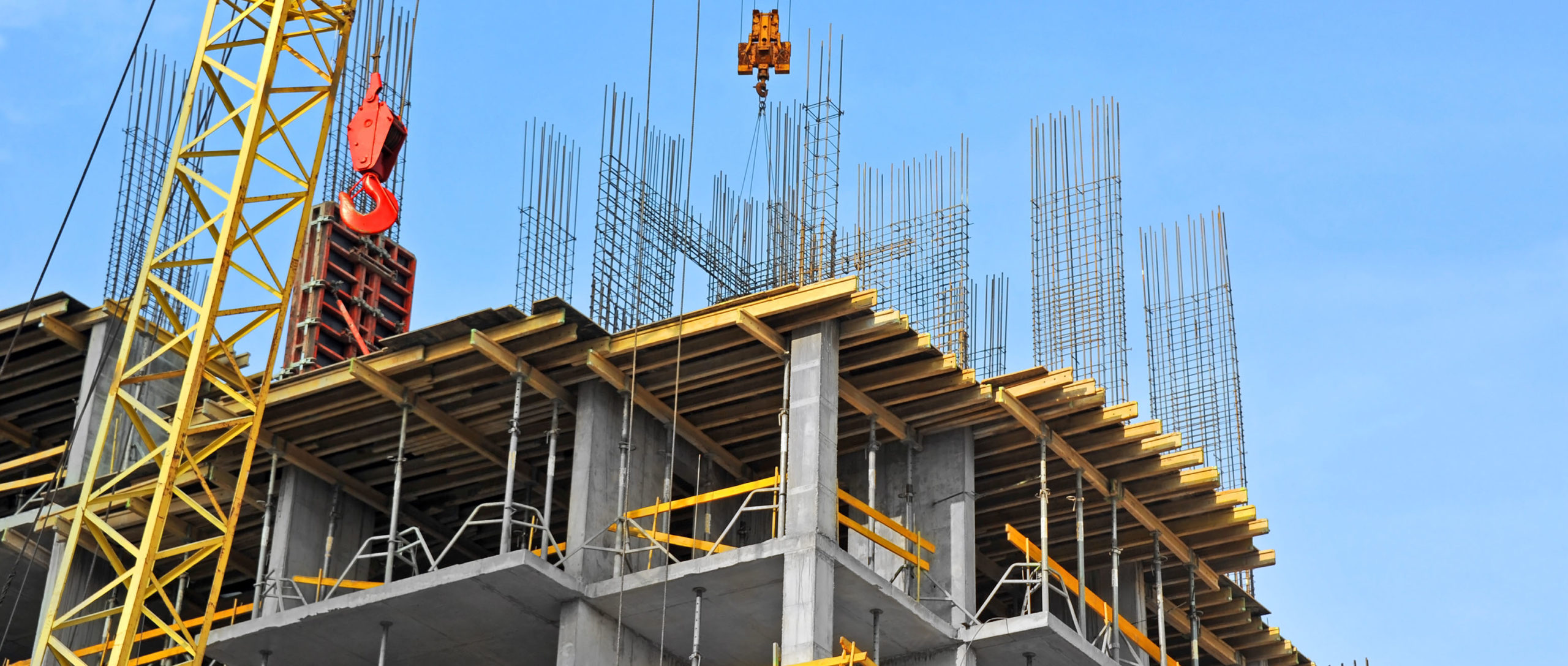
the technology we use
Modern instruments, though reliable, can fail and cause errors to creep in. For this reason, we have compensators to help with accuracy for every site control survey. For example, making sure instruments turn in a true circle rather than an ellipse. All primary control is established by means of a controlled loop traverse with a minimum of two rounds of angles observed.
All our instruments have the current certification of conformity. However, before commencing a project, our site surveyor undertakes instrument collimation checks to ensure nothing’s moved or been damaged during in transit to the site.
Our GNSS control is established with multiple occupation of points (minimum of 45 minutes between occupancies) providing the best accuracy by getting readings to the satellite constellation at different stage of their orbit. We determine the optimum time (often middle of the night) to undertake GNSS surveys where the view of the sky is limited. For example, urban environments, valleys and forests.
Tolerances for all our surveys are discussed and agreed with the client.
points to consider
- As a building takes shape, a robust site control survey will enable it to do so according to the plan. This is particularly relevant with the growing trend for indemnity insurance (£55m+ projects), especially where public safety is concerned.
- We are often appointed to carry out client-requested independent audits – a testament to our attention to detail.
structural monitoring survey
A structural monitoring survey (sometimes called a ‘deformation’ survey) will determine movement using a network of control points located away from the structure itself. There are many different reasons and uses for a structural monitoring survey. They forewarn, provide peace of mind and reassurance. In some cases early detection of the instability of a structure can save lives.
For some projects, we set up monthly monitoring surveys. For example, where a client wants to ensure that a party wall isn’t slipping during a house re-building process or construction of a basement. Then there’s the daily monitoring of a client’s new build to ensure the construction is robust. Some very high profile builds require such surveys. The complex atrium of Portcullis House, for example.
Many structures and buildings require ongoing monitoring to ensure the fabric and structure can be maintained for heritage and safety reasons. Understanding the structural integrity of heritage buildings (such as the Tower of Pisa) is complicated because their deterioration and damage patterns cannot be established visually. Permanent sensor networks equip engineers with the dynamic information they need to understand how a building or structure is coping with the impact of daily life, such as traffic vibration.
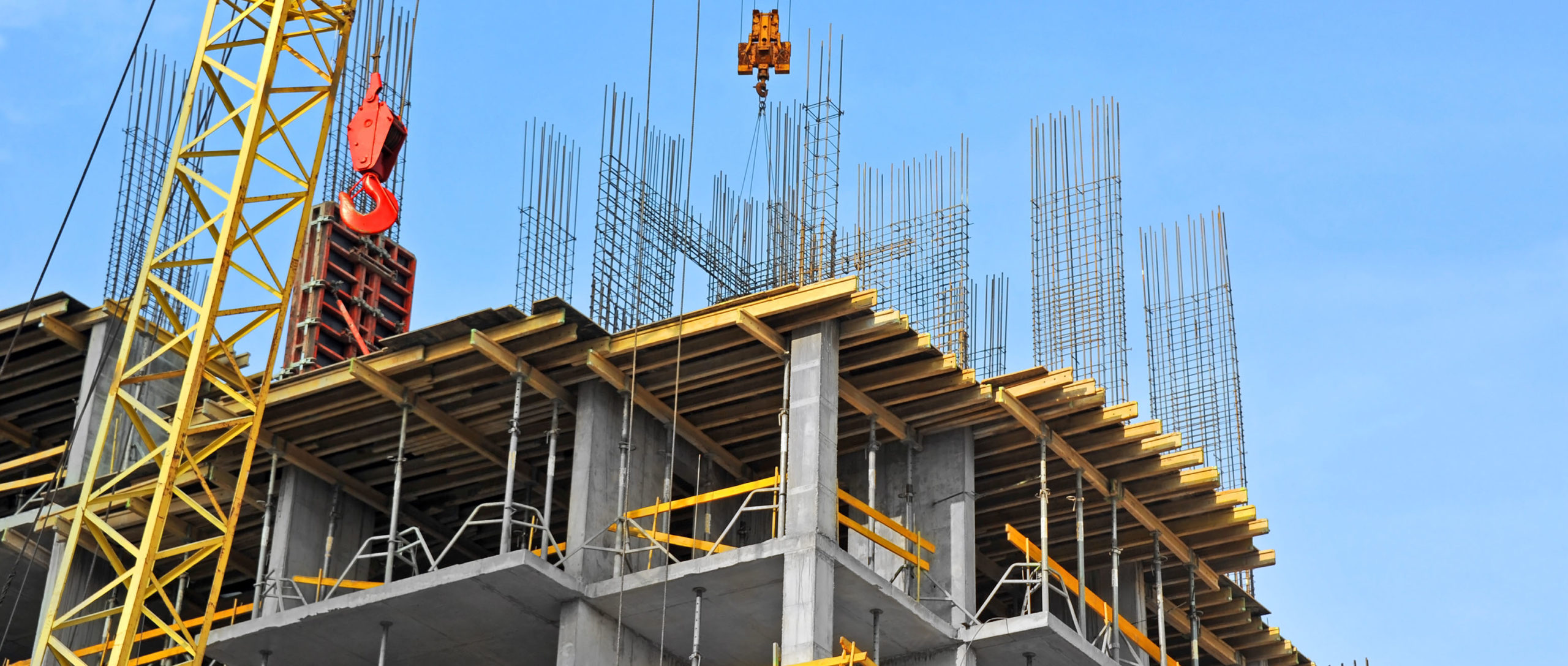
How the structural monitoring survey works
We design every structural monitoring survey to suit the individual needs of our clients. Our aim always is to provide a cost-effective survey that’s relevant to what our clients are trying to achieve. This means understanding their overall objectives and helping them focus in on their desired outcomes so the survey includes the right level of technical information: monitoring duration, measurement frequency, specified accuracies, reporting format, etc.
The measurement of a Transport for London underground tunnel, for example, might prompt us to recommend measurement of pre-defined targets (ceiling, floor, walls) on a frequency of 2-3 times a day. The duration of some structural monitoring surveys are determined by other factors such as ground conditions due to seasonal changes. In such instances, a survey lasting at least 12 months would be necessary to enable the client to make informed decisions.
the technology we use
- Total station
- Time lapse recording
- 3D laser scan dataset comparison
points to consider
Our clients set the objectives of their structural monitoring surveys. For example:
- Noise and vibration
- Crack monitoring
- Precise levelling / settlement recording
- Floor slab deformation
As built survey
The purpose of an as built survey is to highlight whether the project has been constructed correctly and conforms to the site plan. Regardless of the size and scope of the project, an as built survey is invaluable throughout construction – and post completion.
Measuring a building during construction, whether new or refurbished, makes great commercial sense. Is the floor space as anticipated or have the walls moved? Are beams in the right place? Sometimes there’s a change in design – what effect has it had, structurally?
The diligent architect, or project manager, will commission an as built survey several times during the course of a project to make sure the building is proceeding according to plan. It will also measure the progress of construction against the projected timeline for completion. Better to make adjustments during construction rather than risk them accumulating and turning into a costly over runs at the end of the project.
As well as verifying contract compliance, the as built survey also provides a valuable documentation of a building for future reference as it (and its surrounding land) changes.
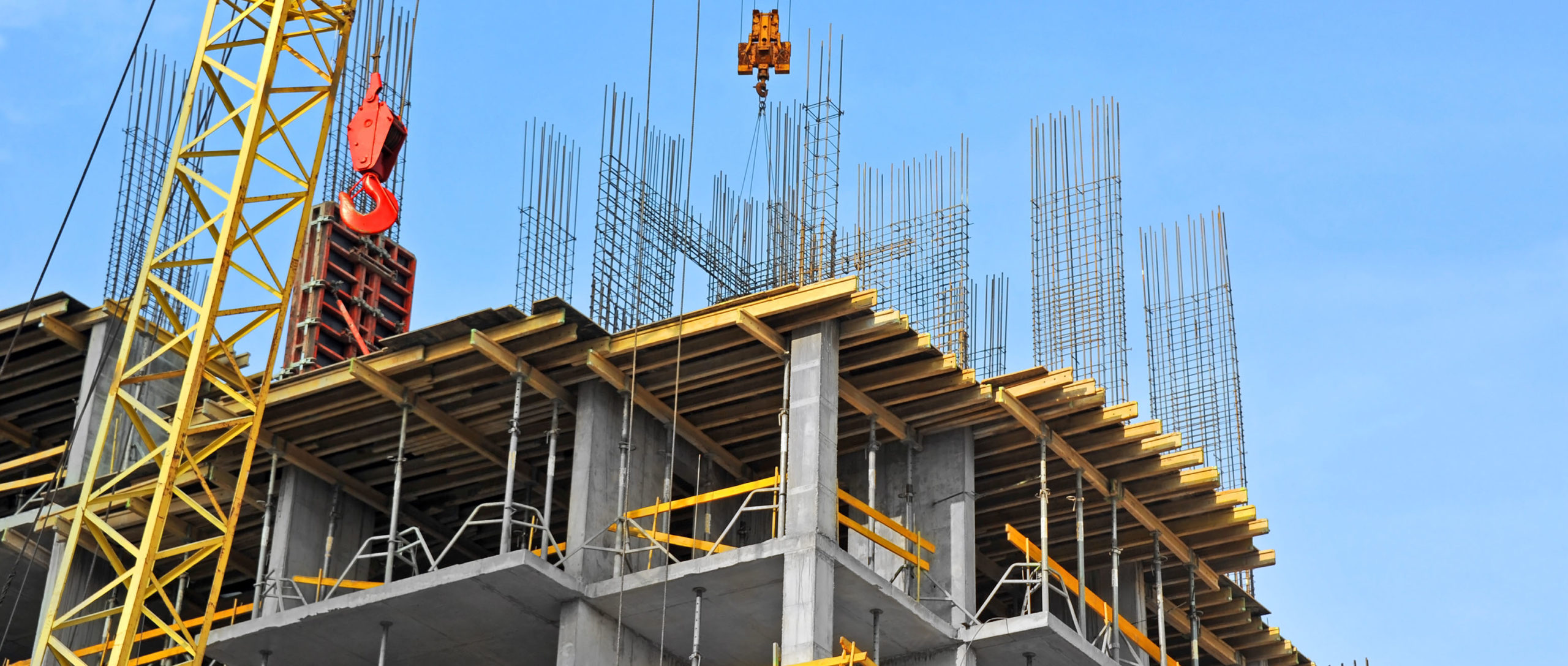
How as built surveys work
As built surveys are undertaken to verify that a project has been constructed according to the approved design – to record and identify accurately any changes. Our as built surveys enable clients to understand the level of completion a project has reached. The construction team can then use the information to extend deadlines and manage remediation procedures.
These are typical situations where the data gathered in an as built survey helps our clients move forward with their projects:
- Land Registry submission (eg updating title plans)
- Retrospective planning approval
- Adoption of highways or utilities
- To obtain a completion certificate for the release of deposits/retention
- To facilitate the re-design, renovation or extension to existing structures
the technology we use
points to consider
As built surveys should be factored in at the start of a project – as part of the initial contract.
A series of as built surveys should be planned (including post completion) in order to monitor progress and record aspects as they are covered up (eg buried services).
As built surveys are best carried out by an independent company to ensure the report is objective and that nothing is missed through familiarity with a project.